- Phased Array is an ultrasonic testing technique that uses specialized multi-element “array” transducers and pulses those elements separately in a patterned sequence called “phasing”. This phasing sequence allows wave steering, focusing, and scanning. This is all performed electronically. The examination can be tailored for each application, increasing speed and reliability of the inspection.
- With the ability to collect and encode full volumetric data, Phased Array brings code compliance and auditable results to the everyday Ultrasonic examination. This makes Phased Array an effective and efficient alternative to Radiographic inspection. And since there is no radiation or environmental hazards, Phased Array inspections can access radiation sensitive areas, increase project production by not displacing other crafts in the area, and maximizes on-site and personnel safety.
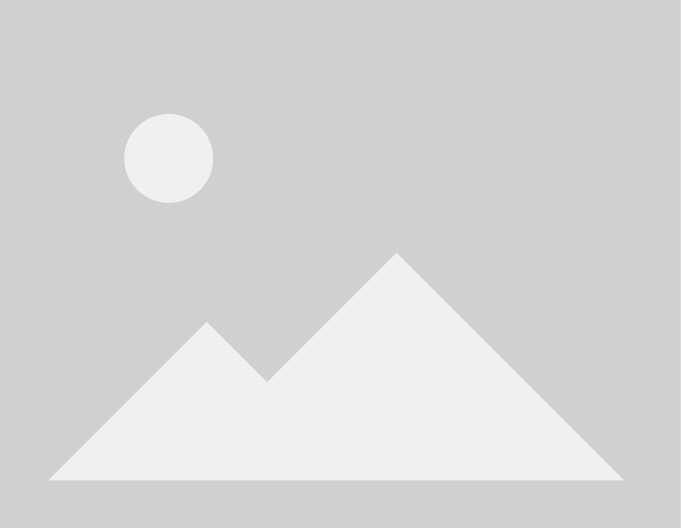
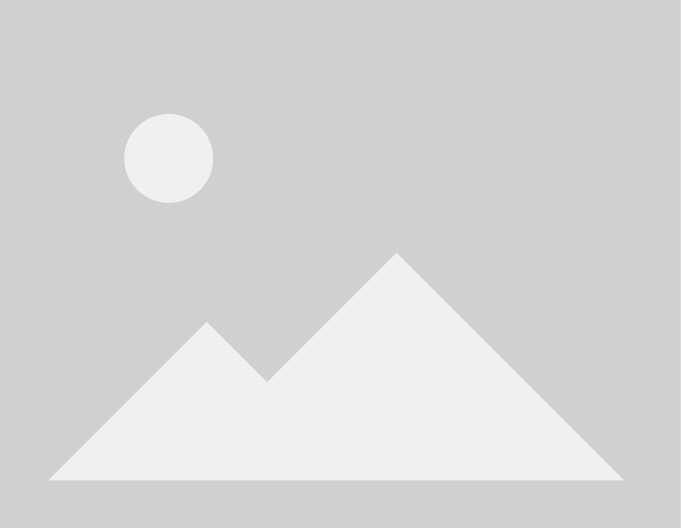
Advantages of Phased Array:
- Excellent repeatability
- Increased inspection speed
- Accurate results
- Ability to inspect complex geometries
- Ability to inspect large areas
- Permanent auditable results
- No safety hazards
Phased Array Inspection Applications
- Petrochemical
- Corrosion mapping
- Detection of hydrogen-induced cracking (HIC), stress corrosion cracking (SCC), and stress oriented hydrogen induced cracking (SOHIC)
- Weld inspection of pressure vessels, piping, and tubing
- Vessels and piping fabricated with composite materials
- Accurate sizing data for fitness-for-service (FFS) calculations
- Power Generation
- Turbine blades and Christmas tree designs
- Pressure vessel and piping welds
- Erosion/corrosion mapping
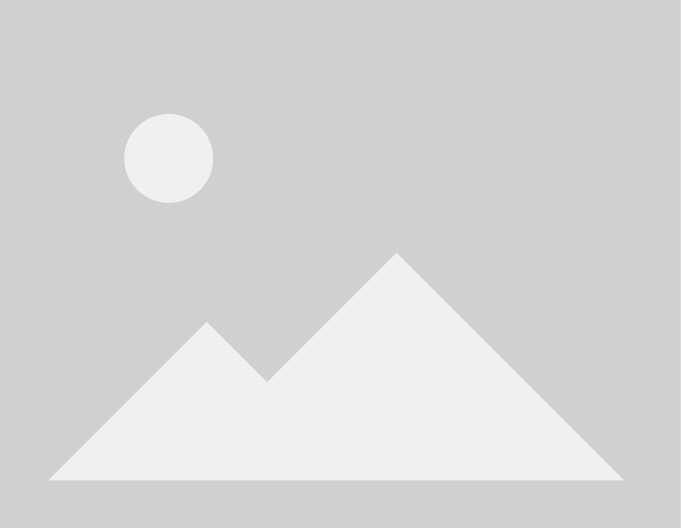
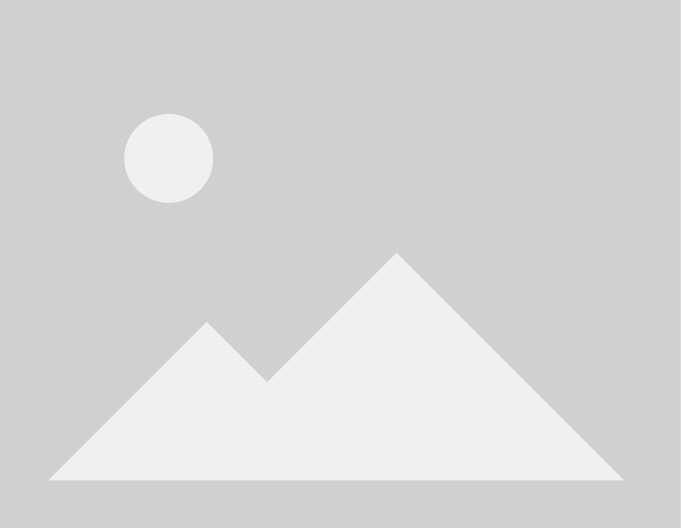
Corrosion mapping
- Phased array testing helps make corrosion inspection fast and efficient. Our solutions enable inspectors to be more productive and collect higher resolution data with fully encoded C-scan imaging.
- The HydroFORM® scanner, FlexoFORM™ scanner, RexoFORM wedge, and Dual Linear Array™ probe offer efficient inspection options for detecting loss of wall thickness due to corrosion, abrasion, and erosion. Our solutions can also detect mid-wall damage, such as hydrogen-induced blistering or manufacturing-induced laminations, and easily differentiate these anomalies from loss of wall thickness.