- Dye Penetrant Testing (PT) is used to find surface breaking defects. PT inspection is suitable for a wide variety of materials, but it is mainly used on non-ferrous metals. This method makes use of the capillary action principle. A liquid dye with low viscosity is applied to the test piece. Due to its low viscosity, it gets sucked into surface-breaking discontinuities. After allowing adequate penetration time, the excess penetrant liquid is rinsed off. After drying, a chalk-like developer is applied. The developer draws the penetrant dye from defects making a visible indication that can be interpreted by the inspector.
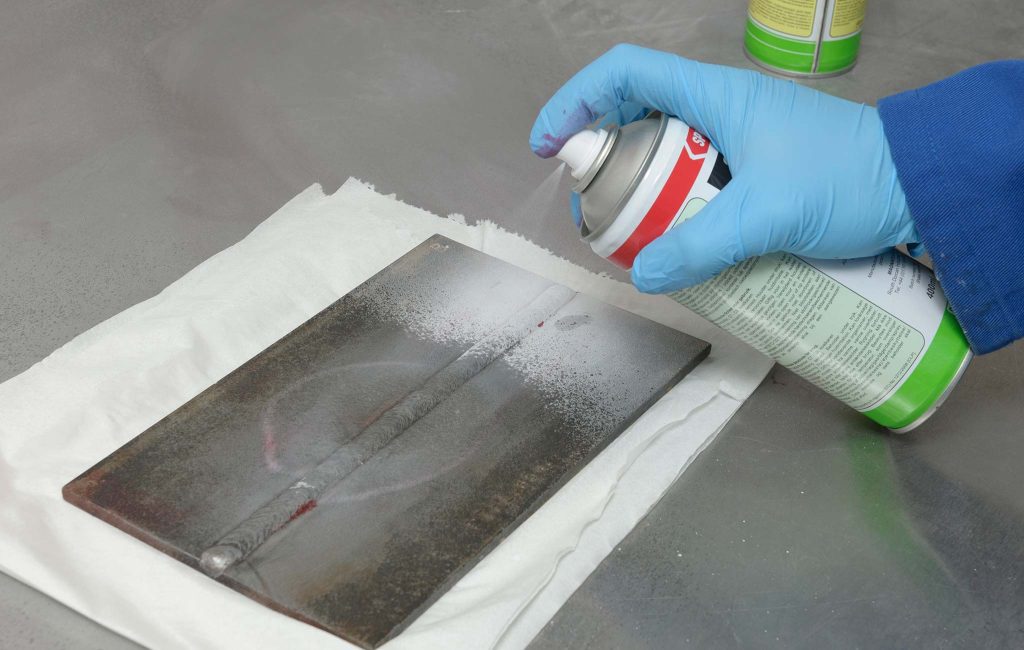
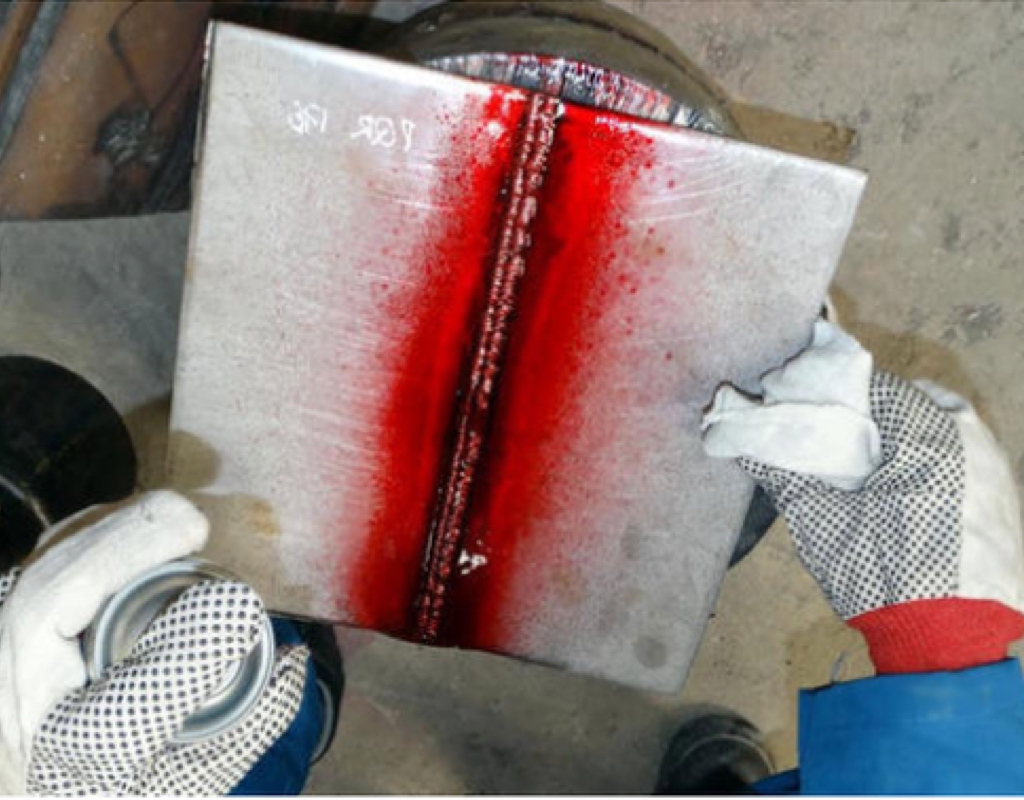
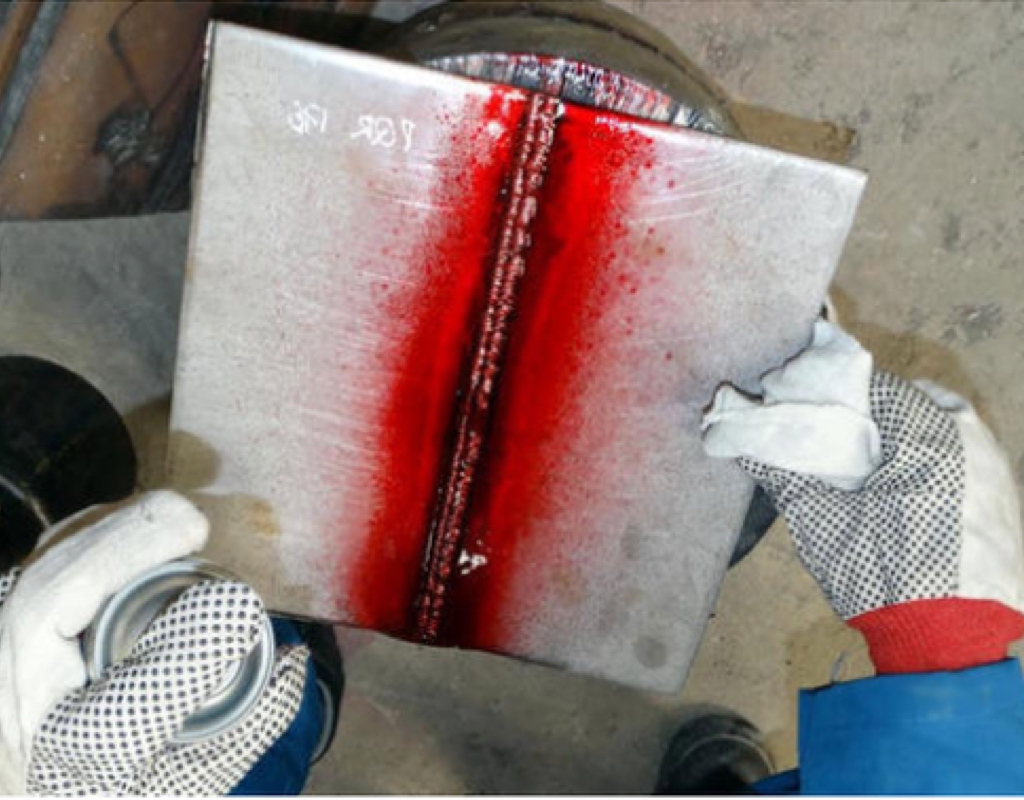
PT advantages:
- High sensitivity to small surface discontinuities
- Suitable for large range of materials: metallic and non-metallic, magnetic and non magnetic, and conductive and non-conductive
- Large surface areas and large volumes parts can be inspected rapidly and at low cost
- Parts with complex geometry can be tested without changing the inspection procedure
- Indications are produced directly on the surface of the part
- Aerosol spray cans make penetrant materials very portable
- Required materials and equipment are relatively inexpensive
PT limitations:
- Only surface breaking defects can be detected
- Only materials with relatively nonporous surface can be inspected
- Precleaning is critical
- Metal smearing from machining, grinding, and grit or vapor blasting must be removed prior to inspection.
- Surface finish and roughness can affect inspection sensitivity
- Multiple process operations must be performed with waiting intervals
- Post cleaning of acceptable parts or materials is required
- Handling and proper disposal of chemicals is required
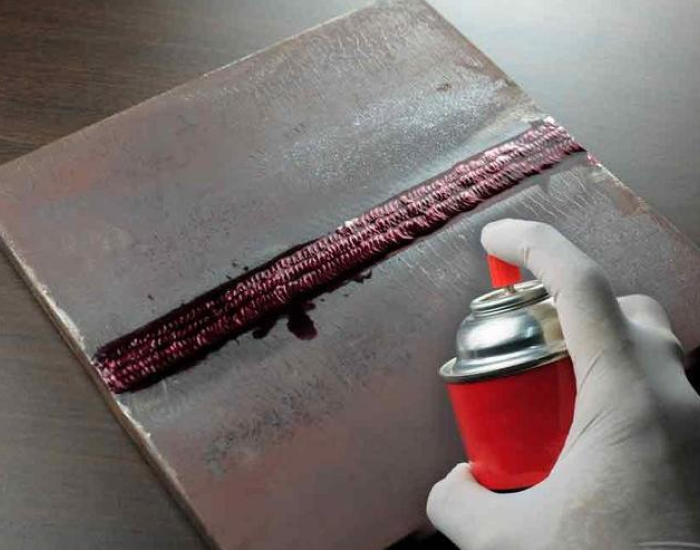
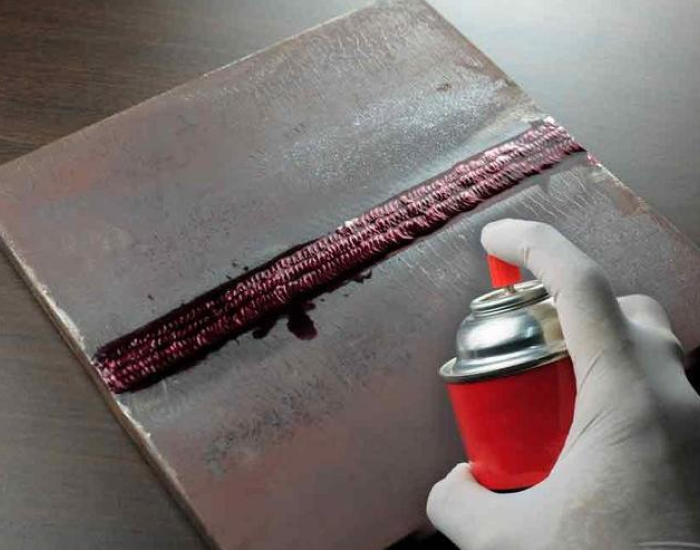