- Vacuum box testing is an effective leak testing technique used to inspect welding joints. This is a relatively fast test and one that can be conducted without interfering with other fabrication operations. The test uses a box fitted with rubber seals around its open bottom and a plexiglass top cover. The weld section to be inspected is coated with a soap-like solution and a light vacuum, usually under 69 kPa (10 psi) is applied to the box. The formation of bubbles on the soaped weld indicates the location of a leak.
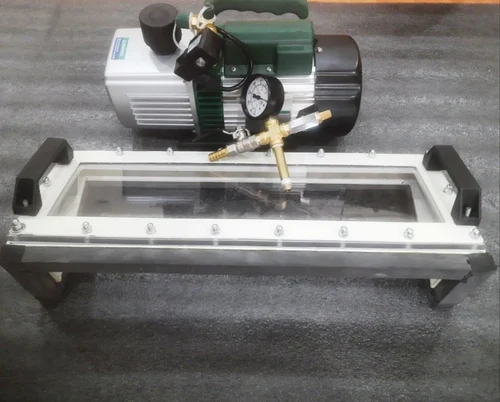
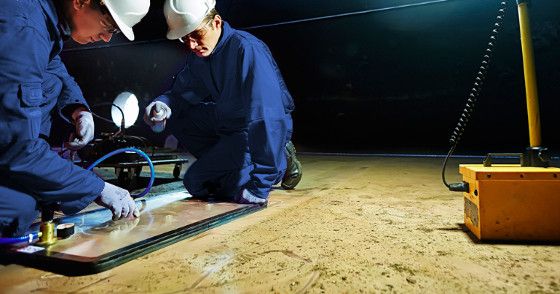
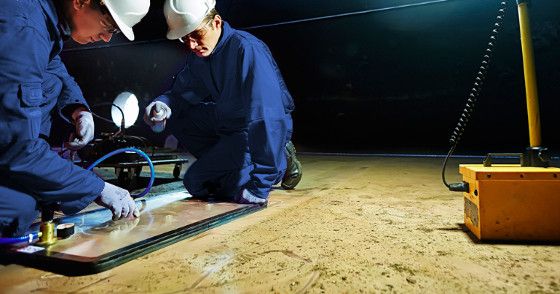
Advantages of Vacuum Box Testing Method
- Provides an immediate indication of any leaks present produced directly on the tested surface
- Easy to use
- Large areas can be inspected rapidly and at low cost
- Can detect small leaks within a given area
- Requires only access to one side of the tested surface
- The method is relatively clean does not require comprehensive cleaning after the test
Disadvantages of Vacuum Box Testing Method
- Can only detect leaks, other welding defects including surface imperfactions are not identified
- Surface preparation before testing including cleaning, de-greasing, rust and slag removal can be time consuming
- The method should not be applied to painted objects
- Size and orientation of any leaks will have to be analyzed with a secondary NDT method
- For standard testing surface temperature must be between 5°C and 50°C. Otherwise, a procedure effective at non-standard temperature range must be demonstrated
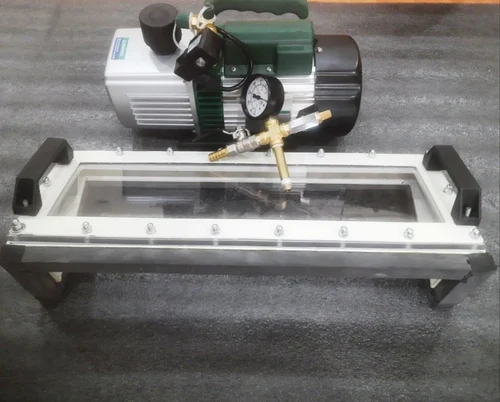